HRCSA: Environmental Considerations
HRCSA’s primary ‘environmental contribution’ is its ability to:
A.) Extend the service lives of steel structures by chemically stopping structure-critical corrosion between crevice corroded and pack rusted joints and connections.
B.) Single component, single coat application saves labor while greatly reducing lane closure time. (less man hours and resources required)
C.) HRCSA polar bonding characteristics allows overcoating (no full removal required) without “lifting” substrate paints. [Durable overcoat system]
D.) No hazardous waste stream (coating lines can be flushed back into original container – and later reused – without wasting any coating or flushing solvent)
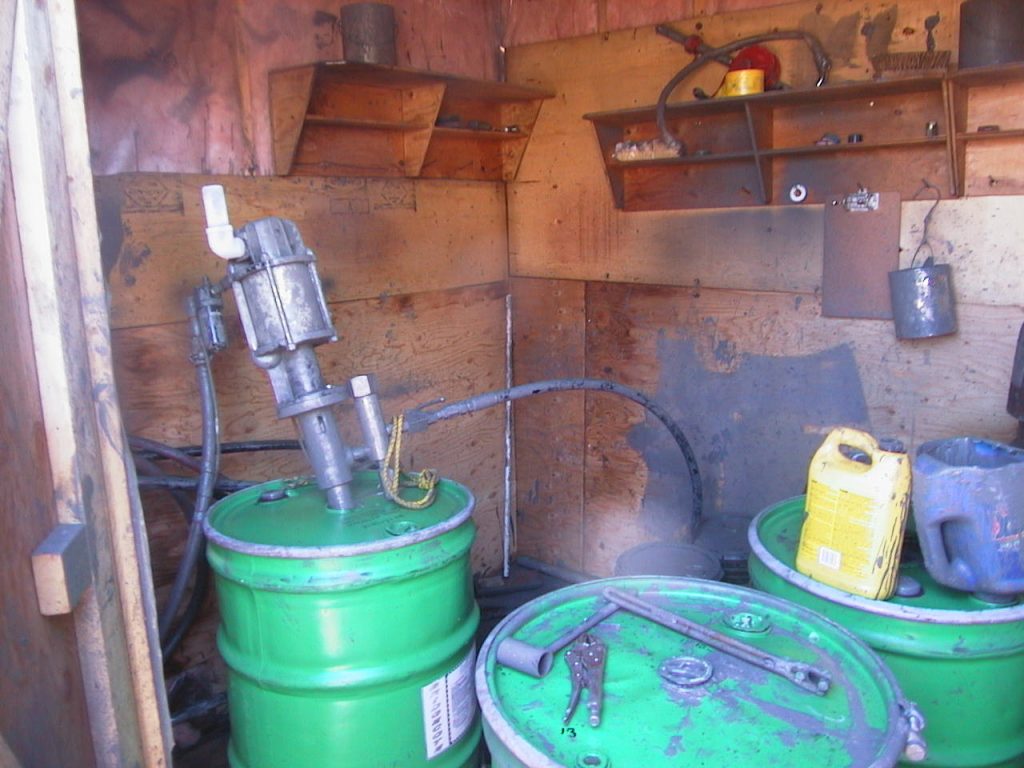
Single component / one coat = zero hazardous waste.
HRCSA is a single component, one coat system wherein one (55 Gallon drum) of HRCSA (Single coat) provides the same coating coverage as 33 (5 US gallon) pails of ZEU (Zinc Epoxy Urethane) packaging.
No HAZMAT disposal for HRCSA: Empty containers can be land-filled.
Being a single component, one coat system, one drum of HRCSA (Single coat) provides the same coating coverage as 33 pails of ZEU packaging.
Zinc-Epoxy-Urethane, multi-coat, multi-component systems requires complex waste management. Example: Three coat paint systems utilize ELEVEN (5-gallon pails) zinc + catalyst + thinner ELEVEN more (5-gallon pails) epoxy + catalyst + thinner, and ELEVEN more (5-gallon pails polyurethane + catalyst + thinner. The total # of pails 33 plus wasted material and solvent.
Compare the above to ONE drum container for HRCSA. [No mixing, flushing lines at end of shift or thinning requirements.]
Three airless pumps in drums of HRCSA supplies nine painters with their one-coat-system [no mixing required]. Empty drums easily scraped clean and the dried coating can be land-filled [no heavy metals or carcinogens.]
HRCSA is best applied by airless spray or can alternatively be applied by brush and rollers [Example: high wind overspray conditions – zone painting.]
Operators need to wear approved vapor filter masks during operations.
With HRCSA polar bonding, overcoating high-pressure water cleaned steel becomes a viable and reliable option.
Containment / Spillage
Containment for the application of HRCSA materials need only consist of the means for managing overspray. Flow-through tarps are gaining popularity.
HRCSA best applied by airless spray and alternatively by brush and rollers.
Operators need only to wear filter masks during operations.
With HRCSA polar bonding, overcoating high-pressure water cleaned steel becomes a viable and reliable option.
HRCSA’s low surface tension, high-pressure water cleaning pressures are kept below the 10,000psi mark and work well on HPWC 5000 to 7000 psi (34.5 to 48.3 Mpa) at 5-6 US gallons (18.9 to 22.7 liters) per minute with a zero degree rotating tip at a maximum of a 4 inch (10 cm) standoff distance to a (SSPC WJ4- NVC3, & NVS10, NVN10) hot water pressure washed surfaces. In these ranges, flow through tarps are effective containment for paint chip capture and overspray management.
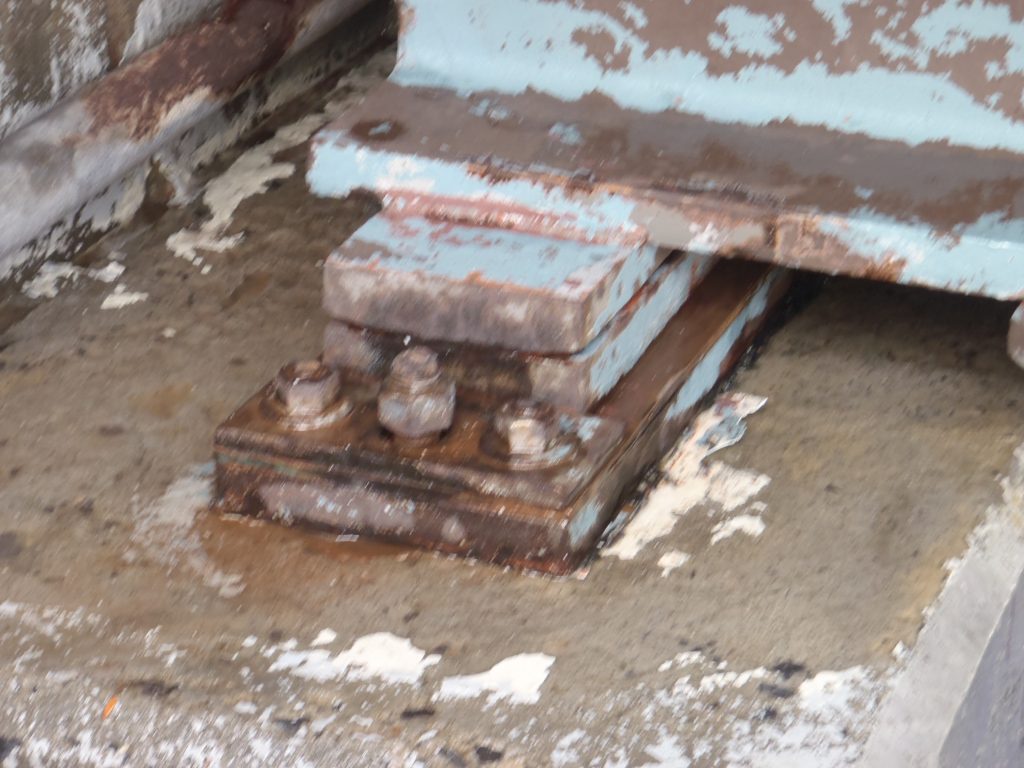
* Typical equipment configurations to drive negative air pressure can burn ~ 1,000 liters of fuel per day.
High-pressure water cleaning equipment (photo) only consumes about 20 liters of fuel per day / per machine producing only a fraction of the emissions a dry abrasive blasting configuration would produce.
Fishkill ratings.
HRCSA is LC50, 96 hours, fish-kill rated at 41,007 ppm. The lower the number, the more toxic the coating materials are. For epoxy or some two-component urethanes, the value ranges from 200 to 400 ppm. HRCSA is the only coating system allowed on bridges that cover salmon spawning rivers.
Wastewater Recovery
In areas where full containment is required to capture and water collection is required, hot water pressure waters can generate ~80% less wastewater as vapors are carried away into the atmosphere.

Collected wastewater is pumped to a flocculating tank, shocked, skimmed, then filtered through 25 microns, 5 microns, 1-micron filtering system.
Filtered water is reused for pressure washing (30% mix). After testing usually can be released into the environment. Residual used wash water most often accepted by wastewater treatment plants.