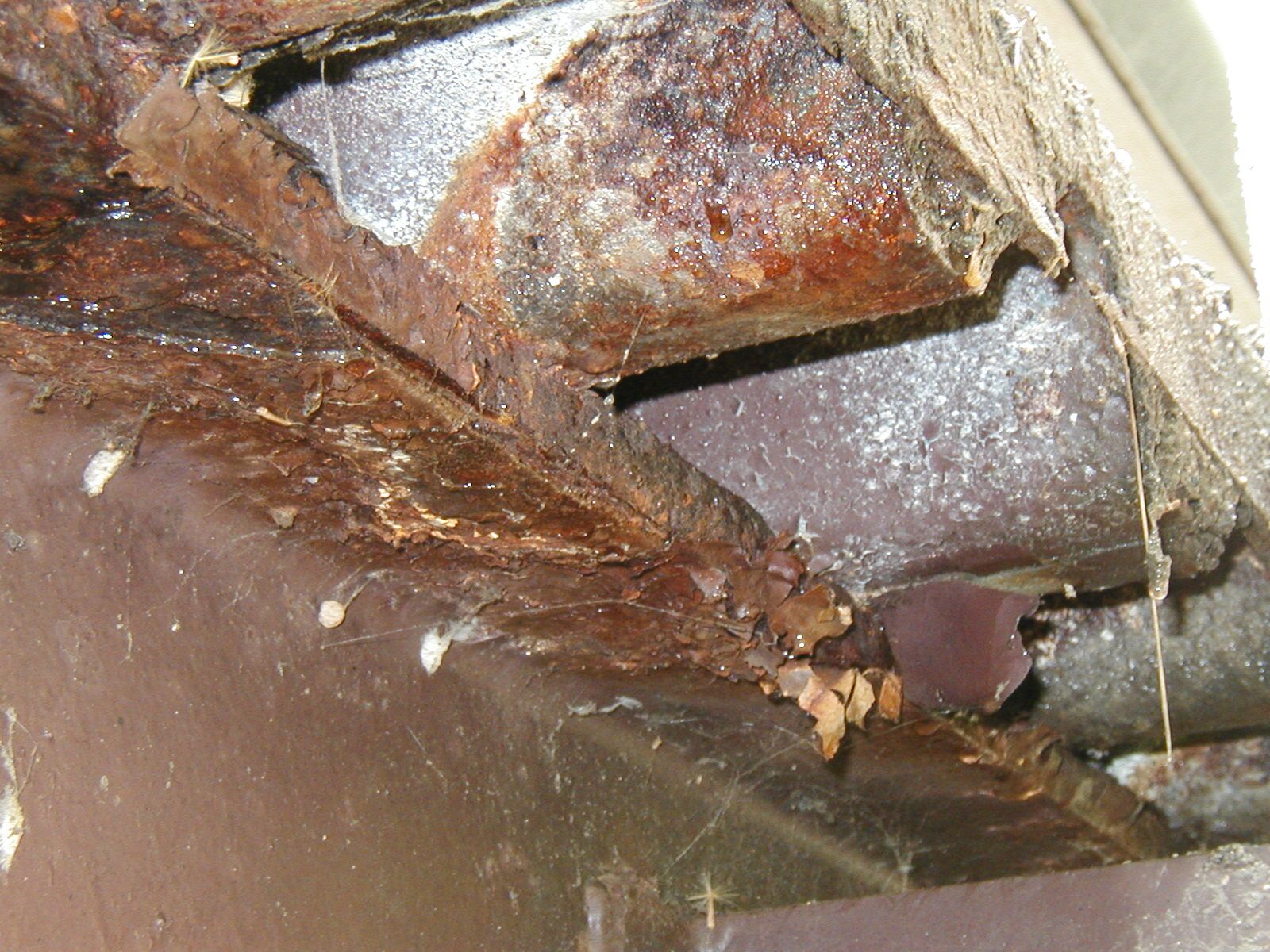
Chemically active HRCSA reacts with corrosion.
HRCSA Coating Failures And Their Cause(s).
Scale rust (black oxides) > 0.4 mm thick.

HRCSA chemistry allows users to black Oxide. HRCSA chemistry triggers black oxide delamination if not removed prior application of HRCSA chemistry.
Where black oxides are tough, crushed glass media injection into the pressure washer spray can be combined to reduce hand tool cleaning efforts.
Osmotic Blistering
“Chemically Active HRCSA’s nature is designed i) displace moisture, ii) scavenge oxygen, iii) neutralize acids at the steel surface, there needs to be enough material present for this to occur. A close look at this photo reveals that HRCSA is way below specification as evidenced by the open gaps between nut and bearing plate.
HRCSA Primer / Topcoat applied to specification would make scratches on the overcoated substrate appear rounded instead of sharp. – a clear example of too thinly applied material.
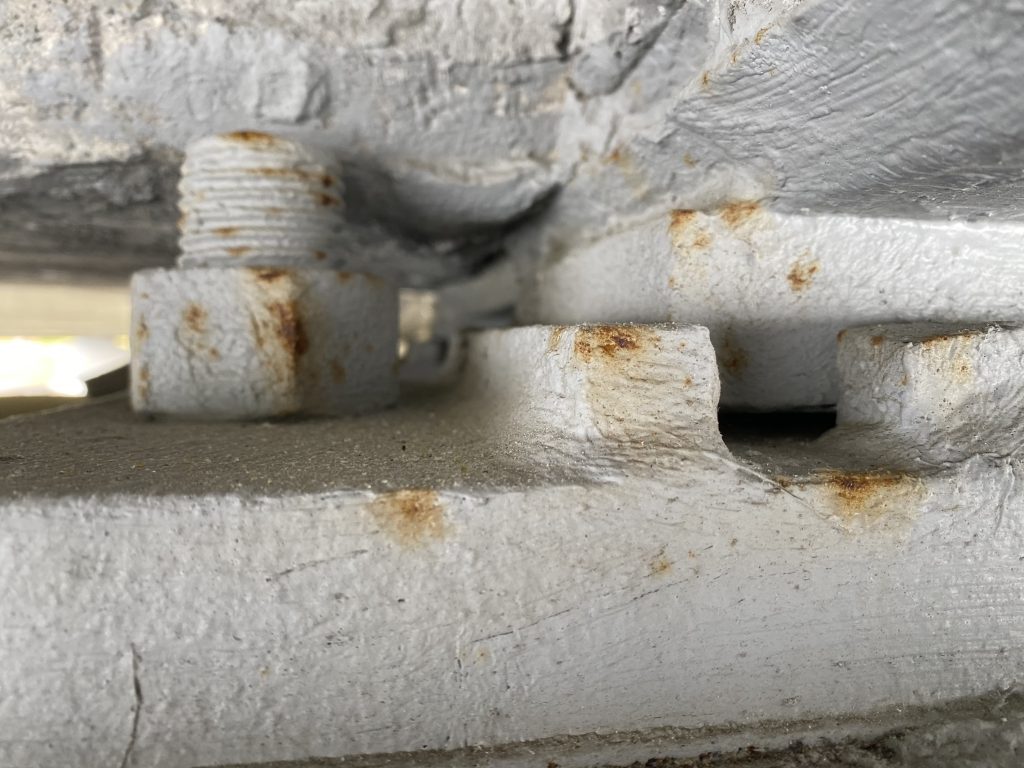
- Moisture passes through liquid applied coatings as matching atmospheric humidity levels

- All liquid applied coatings are moisture vapor permeable (including HRCSA).
- To avoid salts contaminated water between coating and substrate, chemically active HRCSA requires that salts be properly mitigated from the steel substrate (and dried with clean, dry air) before application.
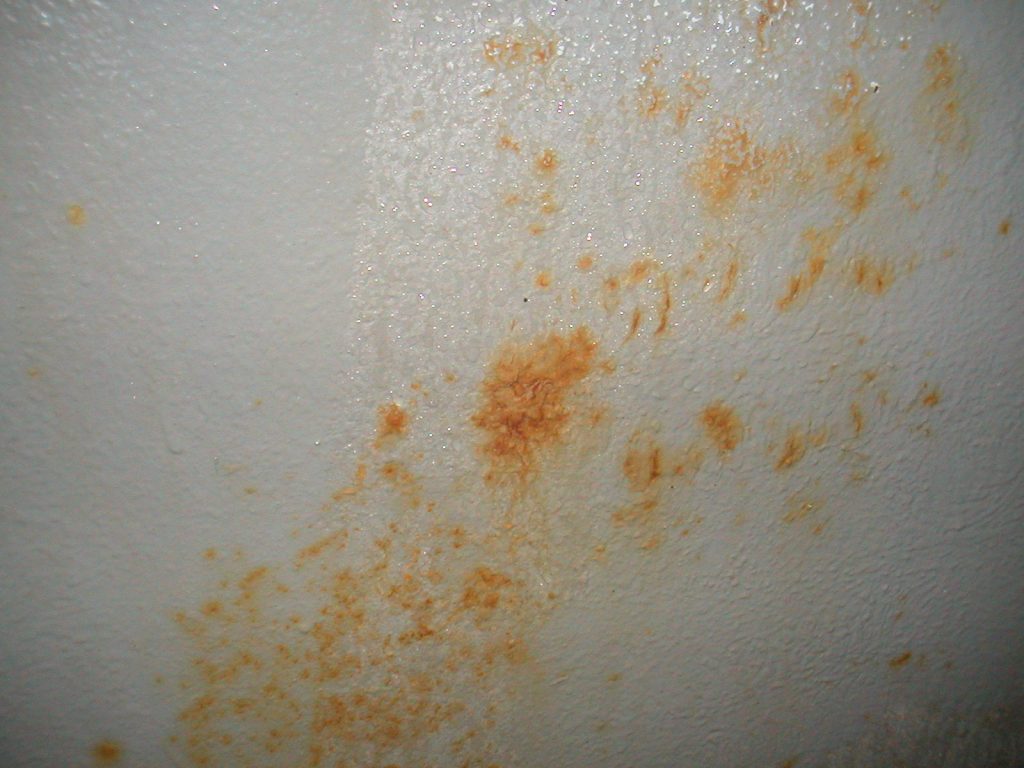
Corrosion bleeding through the applied coating. HRCSA
Missed area.
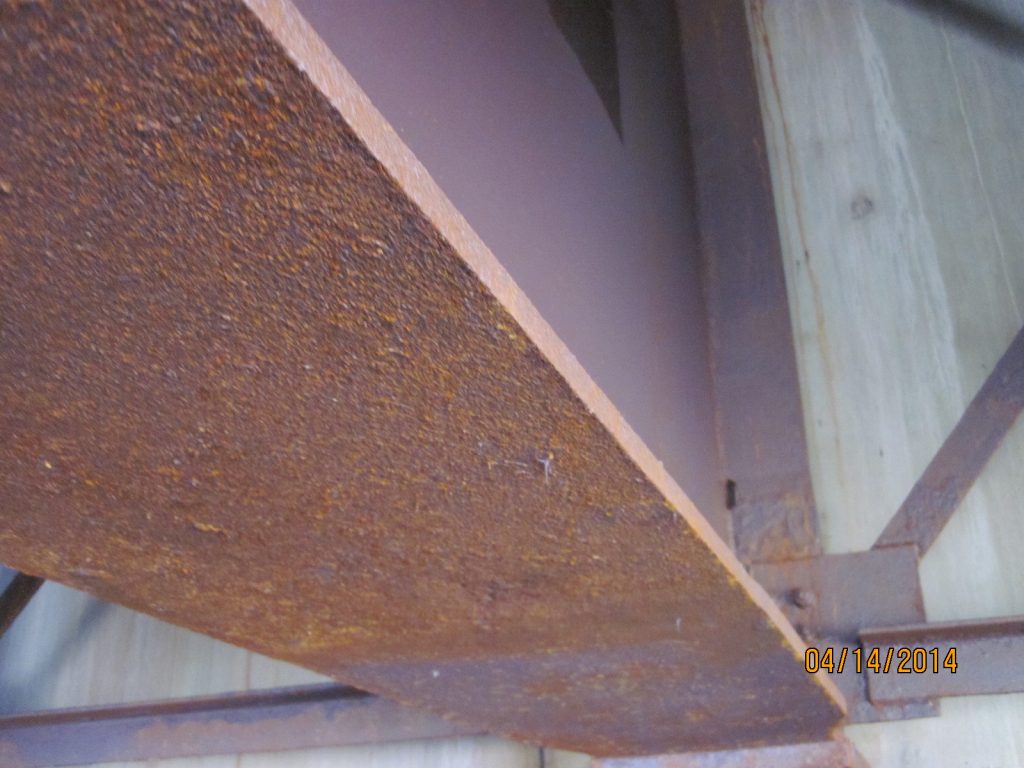
Solvent Blisters
Missed area. Possibly due to poor lighting, access obstruction, etc. The coating application was simply overlooked on this section.
Repair is quick and easy: High-pressure wash with salt mitigation additive / blow dry with clean, dry, high-pressure air / apply TR2100 by spray, brush or roller to specified thickness.
Alternative approach is to buff corrosion using a right angle grinder and scuffing disc, solvent wipe the exposed surface and surrounding coated areas and brush apply a new coat of HRCSA topcoat.
Missed Areas

Pinholes in the applied HRCSAT coating material.
This microscopic view reveals trapped solvent-soaked lint damage caused by contaminant caught on the substrate during unnecessary surface wipe-down prior coating application.
The solvent soaked lint hooked on the steel profile to then creating a solvent bubble which later triggered a pin hole in the TR2100 HRCSA coating system as it evaporated.
To repair, scrape the area where the pinhole exists, solvent wipe with compatible thinner and brush on new coating.
Water Blisters
Pipe condensation at time of coating application is being forced out by the coating.
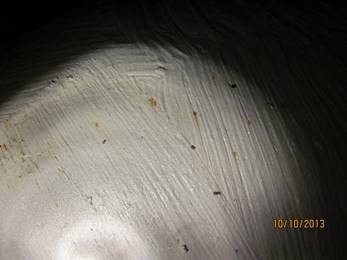
Residual water being displaced away from the substrate by HRCSA active chemistry.
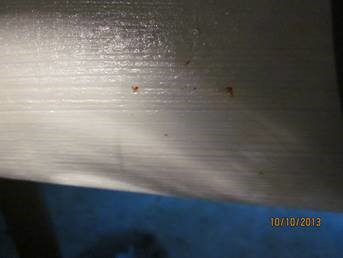
In this example, HRCSA was applied onto a condensation laden (cold) natural gas pipe located inside a non-heated outdoor concrete pumping station amidst 99% humidity.( out of Specification application)

After corrosion was wire-brushed off and salts were mitigated, Thinner was sprayed applied and immediately blown-down to evaporate / dry condensation.
During this short window of dryness, a single coat of HRCSA was immediately applied by brush.
Rust spots indicate residual moisture being pushed out by the coating.
Salt Contamination beneath the coating.
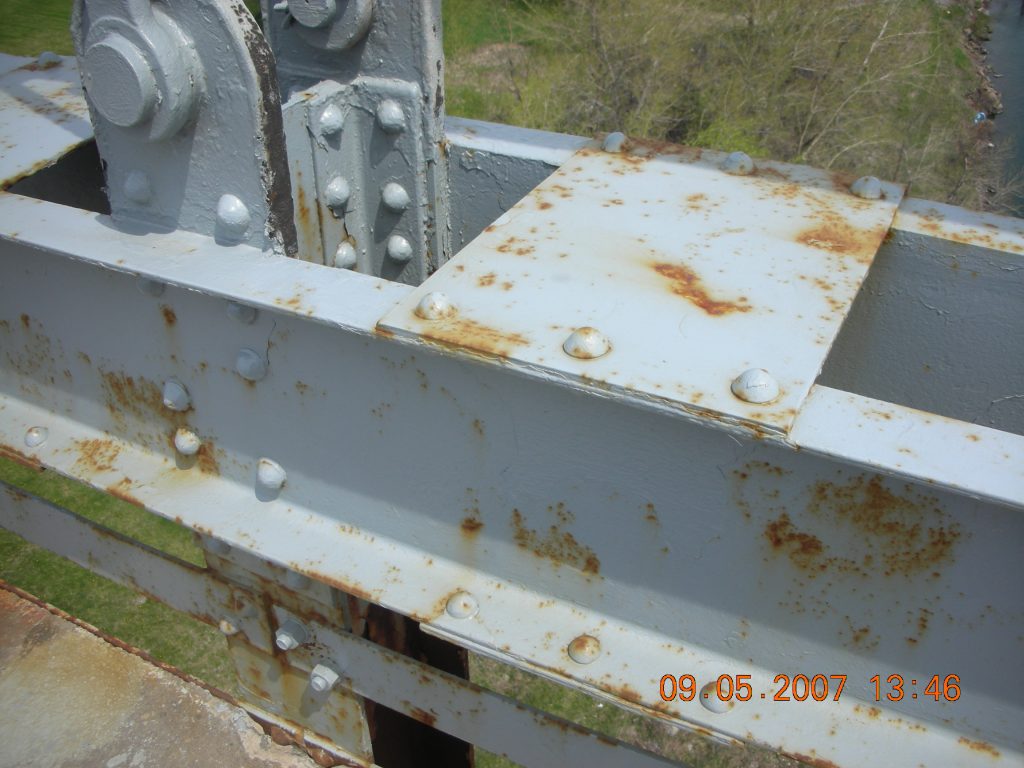
Salts contamination beneath the coating.
Steel can be contaminated during transport, during dry abrasive blasting, from saltwater mists, nearby chemical plants, acid rain, etc. Always test for Non visible Contaminates (salt ions) before applying HRCSA coating systems.
Over-applied HRCSA thickness. [400% Specification]
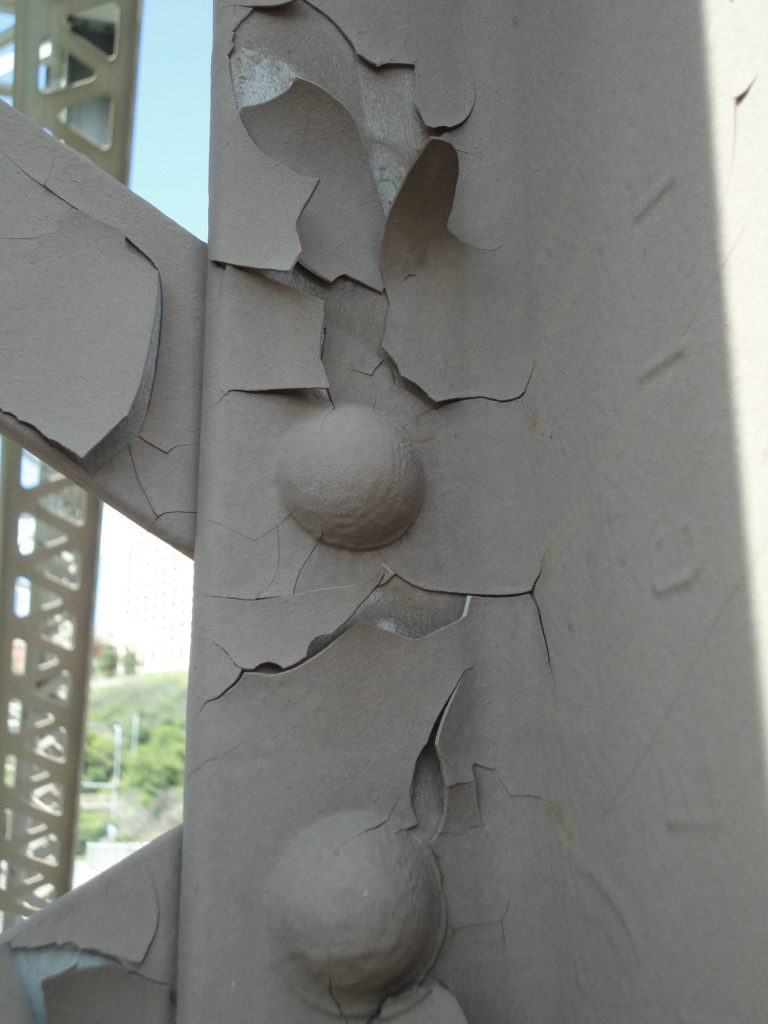
Termarust HRCSA is a one-coat-system. The peeling we see is when the coating was applied to thick. Despite the top layer cracking, note how corrosion is not taking place due to the mono-molecular layer of sulfonate cations that formed on the substrate beneath the coating.
Water not blow out of crevices before HRCSA chemistry applied.

Crevices that have not been blown dry before being treated with HRCSA Penetrant/Sealer will expel the rusty water. HRCSA chemistry displaces moisture, scavenge oxygen, and neutralize acids, corrosion-causing agents are actually being pushed out of the connection.
Fix: Solvent wipe surfaces clean with a HRCSA compatible solvent soaked rag to rid surfaces of existing stains. Stains will not reappear.
Repair Gone Wrong
Broken drain pipes were found to be pouring salt water from the deck onto a bearing. Once repaired, the owner asked for the previously HRCSA coated section to be recoated with HRCSA.
When the repair was done, the contractor did not solvent-wipe the existing coating to reactivate the originally applied material before painting. The end result was 2nd coat of paint peeling away from the previously applied coat.
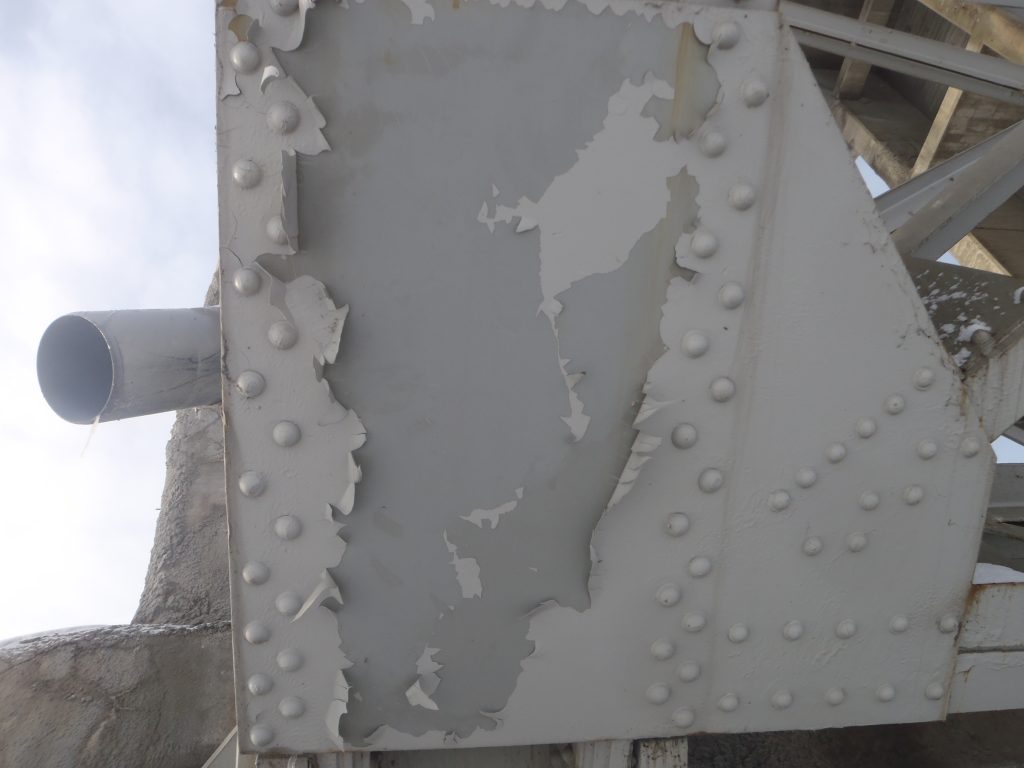
HRCSA Tank Coating Failed Section

During inspection, a section of the coated substrate had failed. The cause of failure was due to HRCSA coating having been applied onto a cold, wet steel substrate.
HRCSA coatings must be applied onto dry surfaces. When applying onto a cold steel substrate (<10C), it is recommended that the coating be brushed or rolled onto the substrate then sprayed over to ensure full surface wetting.