Traditional Barrier Paint Systems…
…Do not Work (on already corroded connections)!
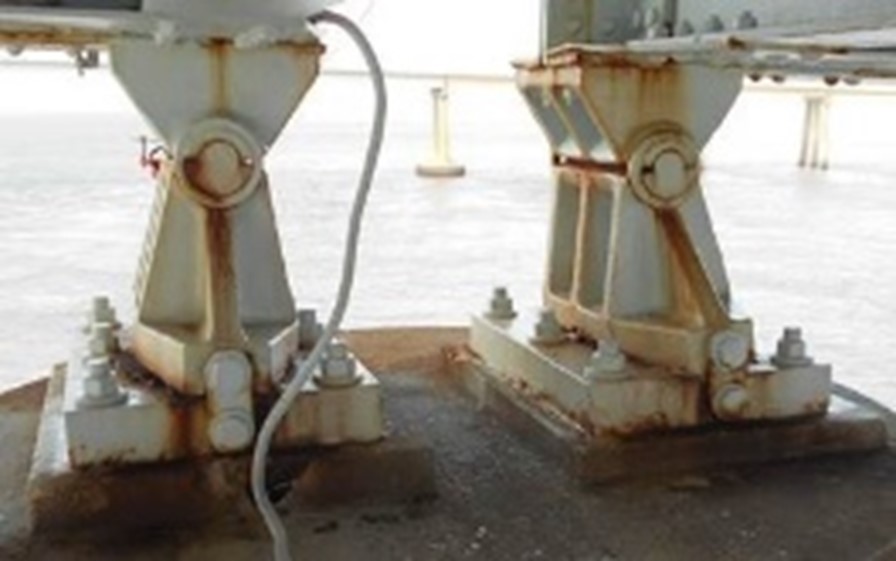
This photo is of bearings which were dry abrasive blasted then painted with a 3 coat zinc-epoxy-urethane system 2 years before.
Active corrosion hot spots continue to fuel corrosion between the plates and inside the bearings thereby converting healthy steel into corrosion by-product within a negative oxygen environment. Covering up such corrosion hotspots with film barriers that do not chemically neutralize the cells only exacerbates crevice corrosion and pack-rust resulting in bent plates and corrosion-frozen bearings.
Corrosion-frozen bearings stress superstructure and substructure elements by impeding contractions/expansions. Anchor bolts sheer, concrete breaks, girders are fatigued.
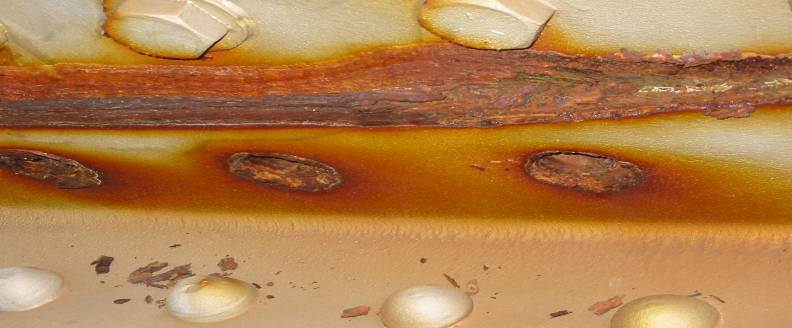
Steel beams can also be affected as corrosion thins steel and corrosion by-product fills connections with pack-rust which can expand to the extent that plates out of plane bend and fasteners break leading to downgraded superstructure load ratings.
“Caulking” chemically active corrosion cells will not stop crevice corrosion. (long term)
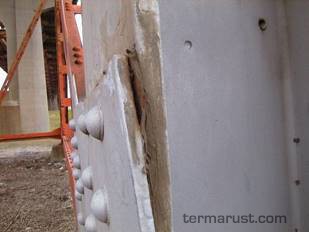
“Applying a 100% solids epoxy penetrating primer followed by the intermediate and finish coast then applying a bead of clear moisture-cured caulking” although commonly specified, does not give you a long term solution.
HRCSA Chemically Stops Active Crevice Corrosion and Surface Corrosion
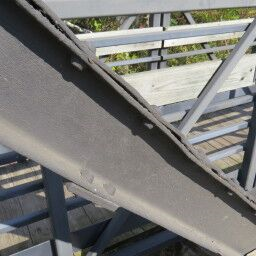
Wire rope, connections, chemically neutralized with HRCSA.
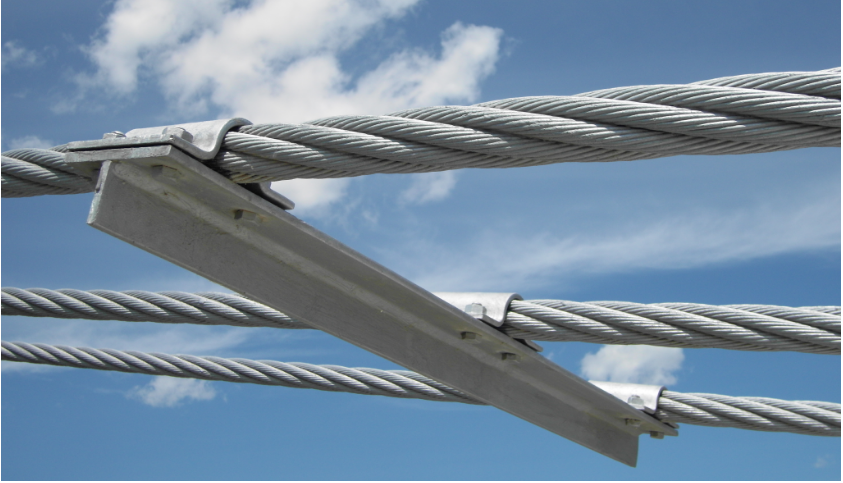
16-year-old HRCSA applied to wire rope. No lifting.
HRCSA is polar bonding – meaning that once applied, this slow cure coating system migrates deep between wire strands, inside pits and crevices before ultimately forming an elastomeric coating that does not microcrack under movement. (Single component – paint mitt applied to SP3 surface preparation.)
Single coat HRCSA
Termarust HRCSA active chemistry: a) breaks the corrosion’s bond with the steel – freeing up the bearing so it can move again, b) displaces moisture, scavenges oxygen, neutralizes corrosive acids at the steel interface and C) lube between bearing plates.
HRCSA Penetrant + HRCSA Topcoat = HRCSA meld coat.
… to form an elastomeric coating which moves with your connection while chemically neutralizing corrosive acids both within and on the outside of your structure.
Chemically stops active crevice corrosion for decades.
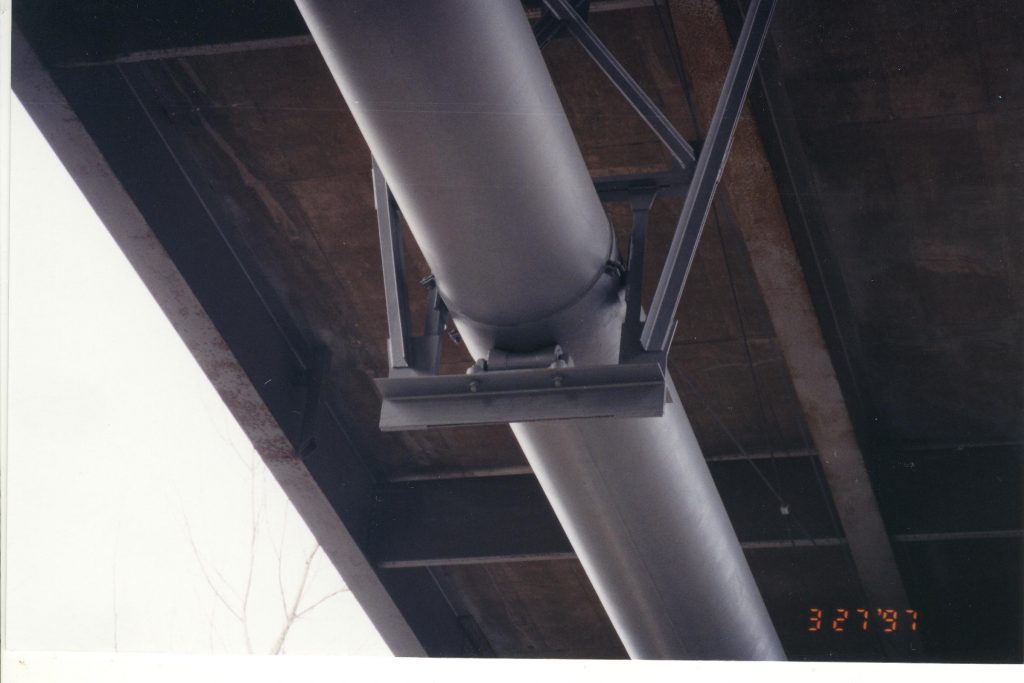
Application procedure:
- Remove non-visible contaminants.
- Dry crevices.
- Pressure apply HRCSA penetrant inside the cervices.
- Apply HRCSA topcoat onto treated crevices with a brush and work the two together.
- Overcoat the rest of the cleaned, dried, structure with HRCSA topcoat.
HRCSA: Outcome Based Solutions.
A chemically active solution offering is only as good as the creative ways they are leveraged to solve a unique problem. HRCSA’s 30 year field history has resulted in a wide variety of solution sets – most of which have not only slashed deployment costs but equally (if not more importantly), EXTENDED THE SERVICE LIFE OF STEEL ASSETS.