Today’s industrial coatings consist mainly of 3 types: 1) Hard film-form, 2) Hard film-form with sacrificial element, and 3) Chemically Active film form coatings designed to chemically stop active corrosion hot-spots.
Transitions
Years of owner prescribed specifications of common traditional hard film form and multi-coat zinc systems have provided engineers with a false sense of belief that “There are no long solutions for crevice corrosion or corrosion-frozen moving parts.”
Applying hard film form barrier coatings to abrasive blasted individual steel components inside a environmentally controlled paint shop will give outstanding barrier protection which lasts.
Applying these same coating practices to already built, aged, corroded, in place structures is not exactly the best performance or environmental fit.
Classic “unsolvable” field corrosion problems when refurbishing aged, in place steel structures.
Field Corrosion Problem #1: Crevice corrosion and pack rust.
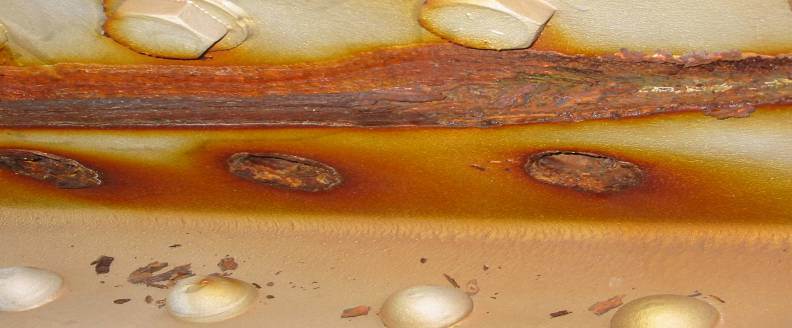
Field Corrosion Challenge #2: Corrosion frozen moving parts.
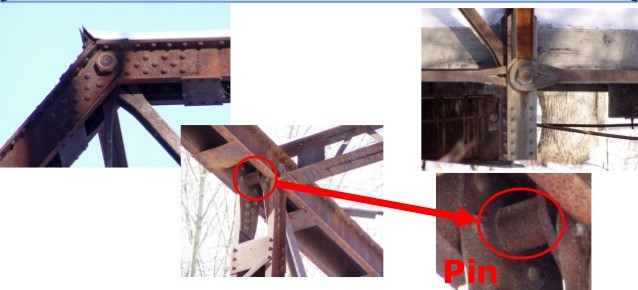
Pin connectors, loaded bridge bearings, bearing pins and other important corroded moving parts need to be freed up, corrosion mitigated, lubed and protected by a chemically active barrier coating that will neutralize the active corrosion and won’t micro crack at the connection.
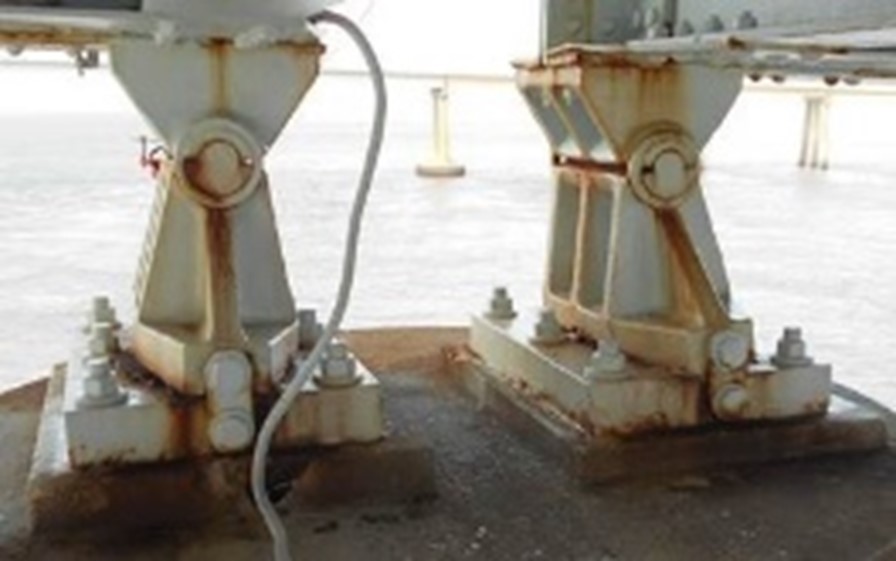
The photo of these bearings 2 years after sandblasting and 3 coat system reveals still active corrosion hotspots that are UNDERCUTTING the applied paint.
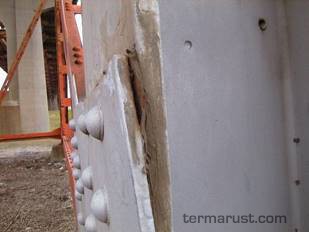
Caulking is not a long term solution. In fact, depriving an active crevice corrosion cells of it’s oxygen ACCELERATES the corrosive activity.
Pits, micro-voids, full surface wetting.

Other aged, in place asset corrosion challenges include:
- Dissimilar metal corrosion /conductivity issues.
- Wire rope corrosion – both inside and outside
- Corrosion inside pipes and tubes,
- others.
Can asking questions – be the answer?

Solution based (Outcome Driven), Performance Based (Performance characteristics of candidate systems), Prescribed (Already known systems).
When it comes to preservation, it’s always good to begin with the end in mind by designing outcome-focused solutions centered around extending the service life of your assets by honing in on structure critical corrosion.
Focusing on outcome-driven specification process can bring about its own challenges like resistance to change with the development of unfamiliar and locally untested solutions. To overcome this, it is important to strive for Win/Win outcomes by identifying the needs of relevant stakeholders and addressing each of their concerns.
Although a people-centric task, let us not overlook the most important stakeholder of all: The asset it’s self. If the Asset could talk, what would IT say about each of the following questions:
Asset: Why are you applying a coating to me?
Engineer: To block contaminants, stop corrosion, and extend the service life of the asset.
Asset: What known causes might explain why corrosion hot-spots keep reappearing in the same areas in shorter and shorter between time refurbishments?
Engineer: Mismatched surface preparation methodologies.
Engineer: Ineffective salt mitigation practices.
Engineer: Coatings applied over active Corrosion Hot-spots
Asset: Do you truly believe that my corrosion cells can be stopped?
Engineer: Corrosion hotspots can be eradicated but only once the corrosion cell has been chemically neutralized. You can’t cover up an active corrosion cell.
Other stakeholders might include: The Engineers, Consultants, Contractors, Public (environmental, lane closures, costs, etc.)
HRCSA: A user-friendly MAINTENANCE COATING field-proven to also chemically stop pit, crack and crevice corrosion hot spots.
1: HRCSA is Chemically Active Part 1
Chemical structure.
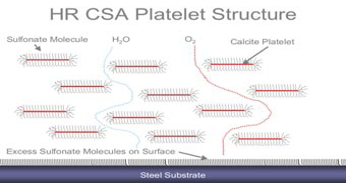
Single component, single coat HRCSA contains the largest volume of active sulfonate and co-polymerized calcite platelets available. Both the Sulfonate Molecules and the Calcite Platelets are polar attracted to steel and when applied to specification, provides FULL SURFACE WETTING both at the steel substrate surface and inside the pits and micro-cracks of the substrate.
HRCSA calcite platelets serve two purposes: 1) Creates a “snake skin” like barrier that slows the ingress of moisture and 2) will sacrifice themselves
Micro-voids between the film former and the steel substrate become a thing of the past.
Undercutting of the paint can become a thing of the past.
When


2: HRCSA is Chemically Active Part 2 Structure Critical Joints and Connections
HRCSA Penetrant [Pressure applied ONLY inside opened connections, packrust cells, between plates, etc. is a low viscosity, chemically active material used to chemically stop crevice corrosion cells. Pressure applied into clean, dry, open connections and topcoated with HRCSA Topcoat produces and elastomeric seal which works its way deeply into capillary channels until the internal parts of the cavity become as coated as the outside of the cell.

HRCSA Part 3: Elastomeric, non-conductive (up to 750 kva), low surface energy.
SIngle coat HRCSA topcoat can be applied by spray, brush or roller onto clean, salt-free bare steel or clean, dry, salt-free, tightly adhered coatings.
- HRCSA is low-surface-energy bonding meaning that it will tug and lift overcoated substrate paints. This also means that HRCSA performs exceptionally well in severe freeze-thaw climatic conditions. Low surface energy bonding also means that HRCSA is super user-friendly and surface tolerant when applied onto light to medium flash rusted steel.
- HRCSA is elastomeric. Cured HRCSA topcoat stretches up to 700% at 25 micron thickness (90% at 100 microns DFT, etc.). This means that HRCSA topcoat will not micro-crack when applied on pins, plates, etc.

HRCSA is non-conductive – great for isolating against Galvanic Corrosion. This characteristic is especially appreciated wherever dissimilar metals meet. [Galvanized bolts on hardened steel, etc.]
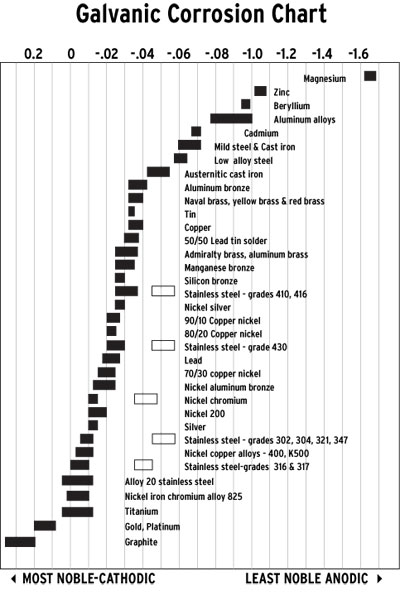
HRCSA is User-friendly, surface tolerant.
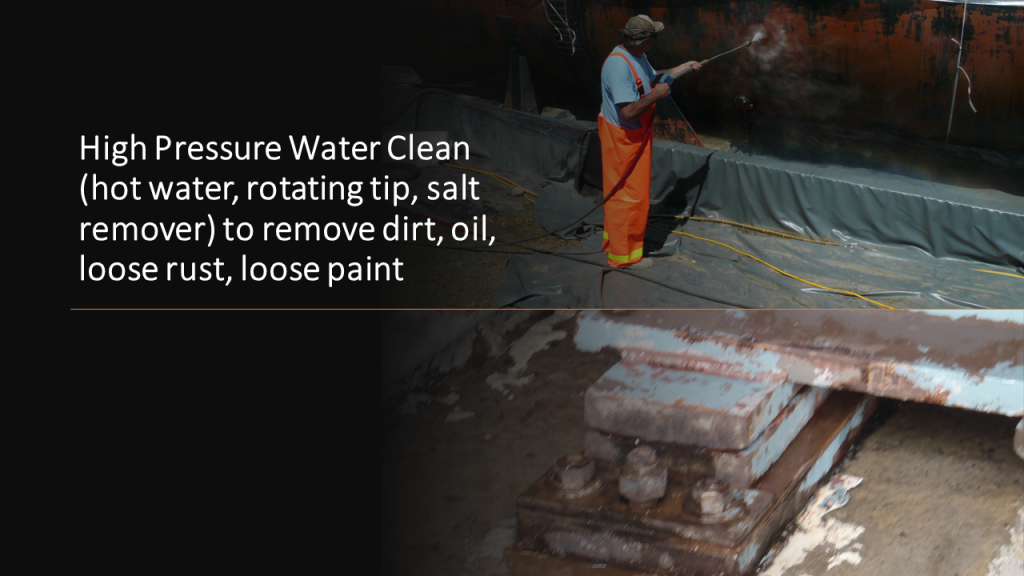
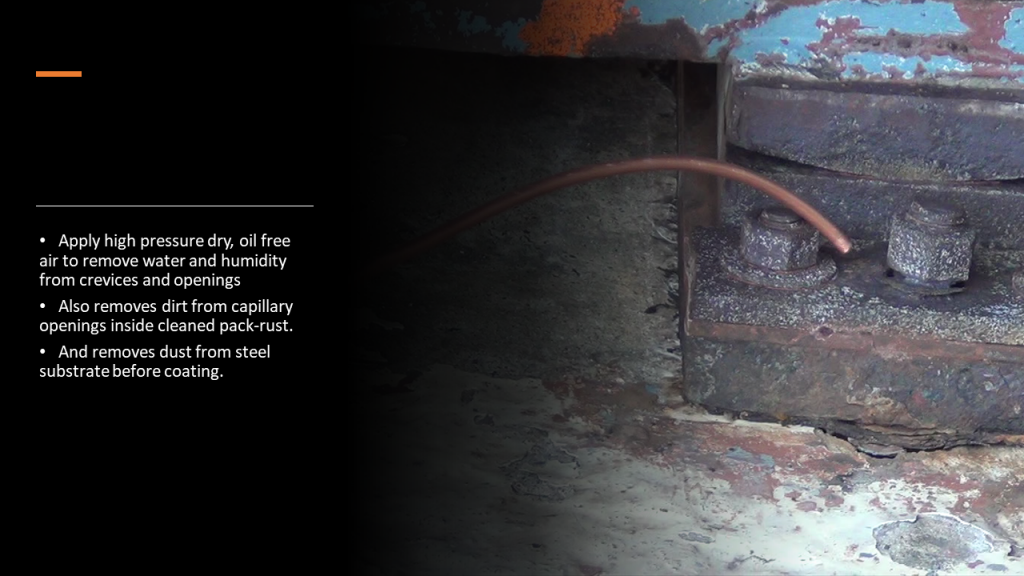

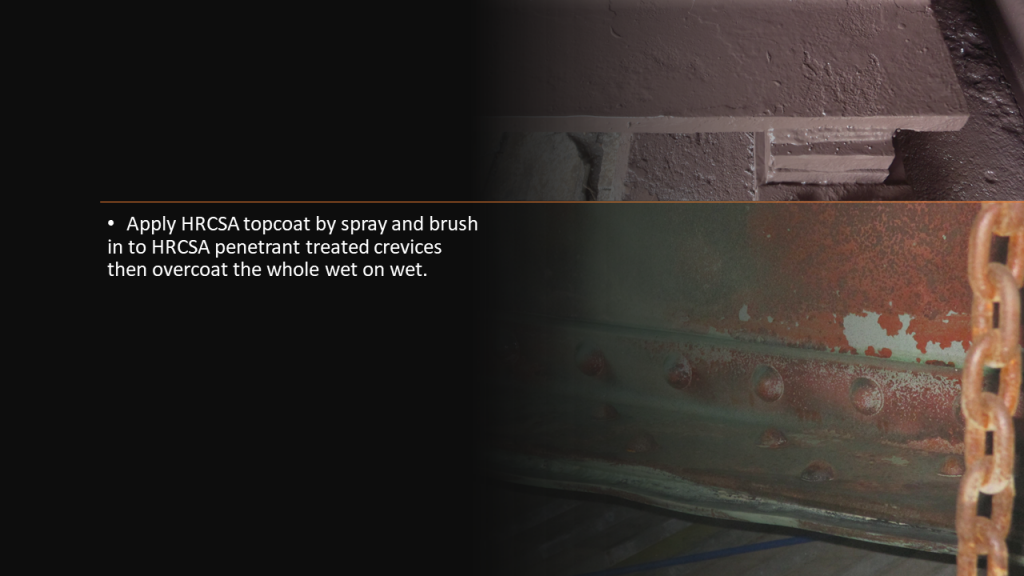
HRCSA on pipes and wire rope.

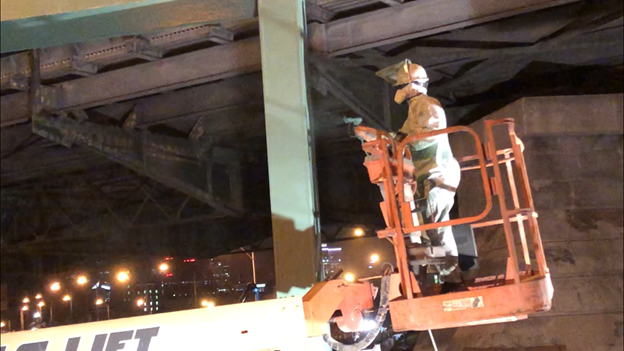
HRCSA is a single coat, single component system best applied via airless spray.
Case Study: Edmonton High Level Bridge
