1. High Pressure Water Cleaning WJ4
The steel substrate where HRCSA chemistry will be applied are to be cleaned using a [7,000 psi 6 gpm (48 kPa, 22.7lt/m) Hot Water pressure washer– with a zero degree rotating tip (at a maximum of a 4” (10cm) standoff distance)

BEFORE: Photo of corroded steel substrate prior to high pressure water cleaning

On surface areas where black oxides do not come off during pressure washing, the black oxides must be removed (needle gun, pneumatic gun, chipper hammer, media injection, etc.) and bonded surface salts removed.
Example of High Pressure Water Cleaning with 7,000 psi, 6gpm hot water, rotating tip.
AFTER: Photo of same steel substrate after high pressure washing. Some handtool cleaning was necessary for removing firmly bound block oxides at the outer edges ~ 1% of surface area.

Acceptable surface preparation – all loose paint, loose rust, and surface black oxides have been removed.
Salt Mitigation
Salts can be removed during the surface preparation or after a WJ4 (or SA2.5) cleaning and accessible black oxide removal.
Salts can be removed during the surface preparation or after a WJ4 (or SA2.5) cleaning and accessible black oxide removal.
Non visible Contaminants (NVC, NVS, NVN) Salt measurements are not to exceed NVC3 3ug/cm2 [chlorides], NVN 10ug/cm² [nitrates] and NVS 10 10 ug/cm² [Sulfates] levels on flat surfaces and a thorough flushing of all opened connections and pack-rusted connections.
Drying
HRCSA chemistry can safely be applied overtop light to medium flash rusted surfaces. Blow down the substrate with clean, dry, oil-free air – PARTICULARLY INSIDE CONNECTIONS AND THOROUGHLY WASHED (with salt remover) PACK RUSTED AREAS before applying HRCSA chemistry.

Blow pipes ¼ inch copper for blowing water from inside joints, connections and bearing faces. Large bore pipes are used for removing dust from large surfaces. (Long waiting periods after pressure washing took place – but before applying HRCSA).
2. Abrasive Blasting SP6, SA2 (Option)
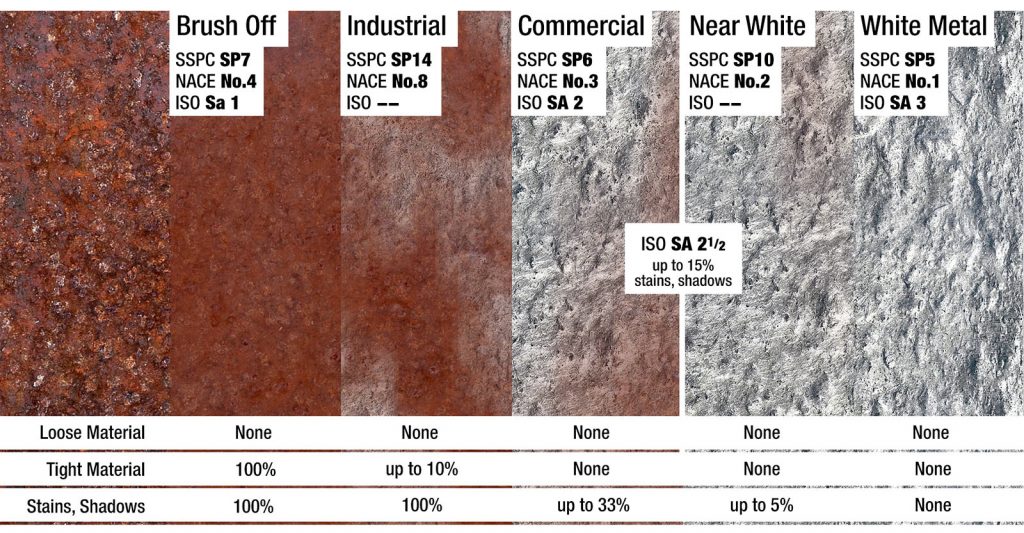
Where specifications call for Dry Abrasive Blasting, a pressure wash with salt remover additive is often still needed to mitigate corrosion hot spots.
University of Kentucky corrosion hotspot case study:
“SSPC-SP10 dry abrasive blasting is the least effective method for removing corrosion hotspots” 11m55s: https://www.youtube.com/watch?v=NKir-6fPM_8
WAB: Wet Abrasive Blast (Option)
The 24 hour corrosion hot-spot test
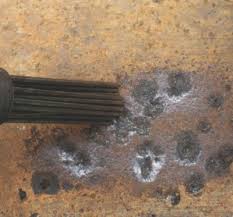
Despite the appearance that pit corrosion looks clean following a high pressure wash or abrasive blasting, ionic bonded salts at the bottom of the pits very often continue to be present.
Best Practices encourage exposing cleaned (pressure washed or blasted) steel to the elements (air and humidity) for an additional 24 hours. Active corrosion hot spots will darken indicating active corrosion hotspots still need to be treated. Flushing the bottom of the pits with high pressure water cleaning (hot water if possible) with salt remover is the solution of choice for final corrosion hot spot mitigation.
NACE Paper on OSMOTIC BLISTERING.
NACE Paper on Osmotic Blistering
3. Managing crevice corrosion, pack-rust
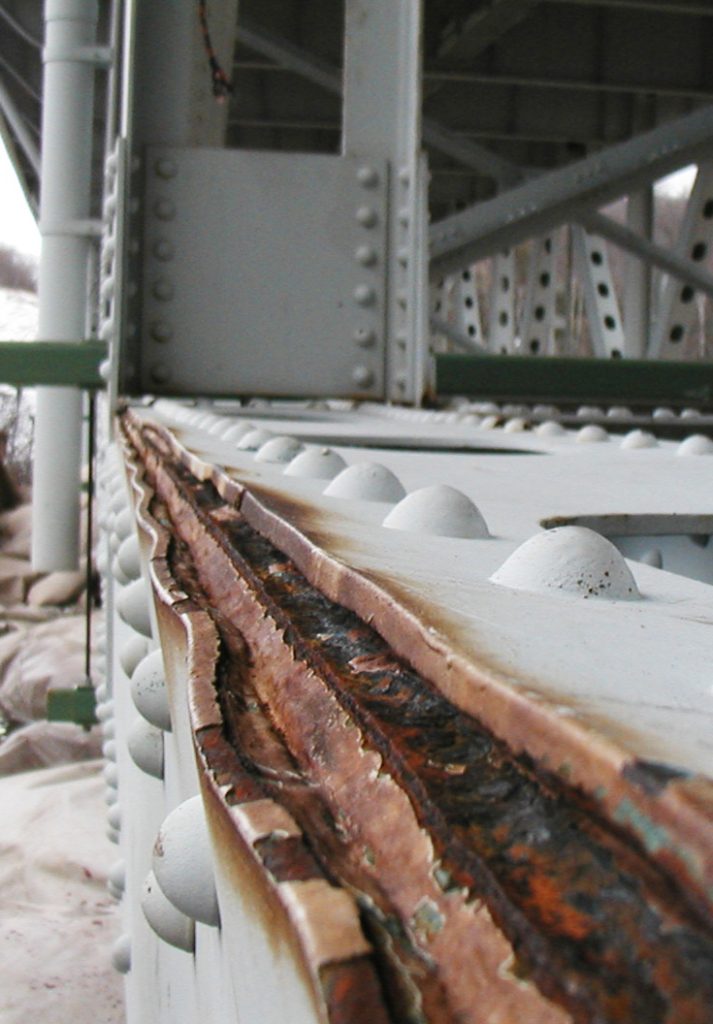
Crevice corroded and pack-rusted joints and connections should NOT BE ABRASIVE BLASTED
1.The black oxide in the joint is chemically neutral and must stay in the joint as it is now part of the joints structure.
2. To avoid risk of clogging the veins and pores. Where abrasive media is being introduced to clean the substrate, the manufacturer recommends that the crevice corroded joint areas be taped off before blasting.
Thoroughly flush embedded pack-rust with high pressure water cleaner (rotating tip) and salt remover.
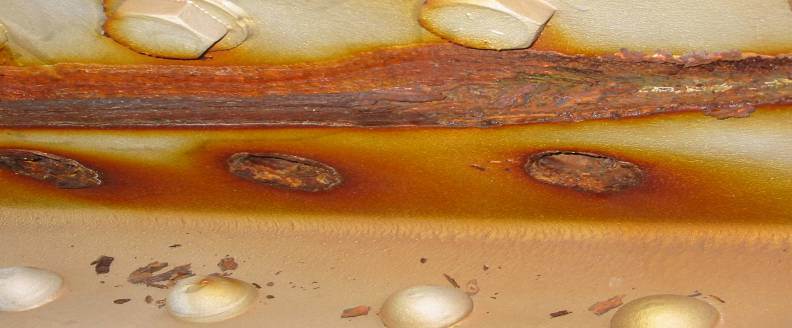
Pack rust material may appear solid but consists of small voids or path ways in the corrosion by-product. HRCSA cleaning requires that all areas inside connections be thoroughly flushed with high pressure, hot water with rotating tip and salt remover additive. This action will: clear out corrosive acids (best effort), remove loose material, and open up capillary channels inside the pack-rusted areas. Once cleaning is complete, a blast of high pressure compressed air (clean, oil-free) will remove any remaining water, loose matter and open up capillary channels inside the pack-rust. These open voids will act as reserve channels when HRCSA Penetrant/Sealer is pressure applied to the opened connection.
Targeted Outcome
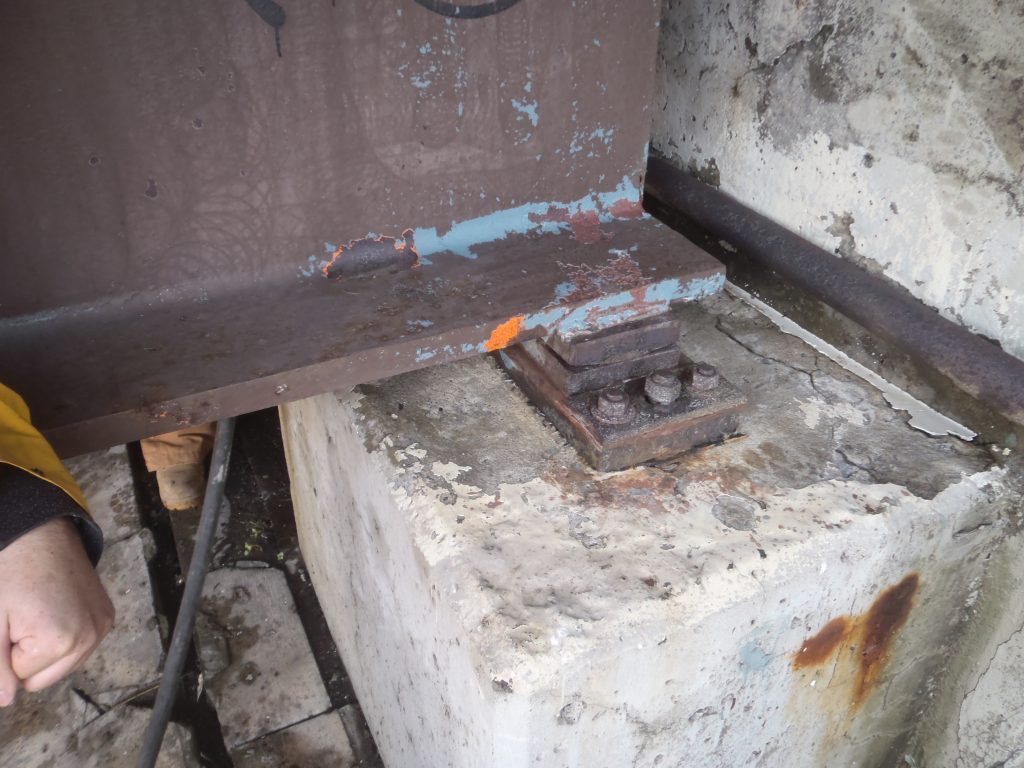
Corten Steel [A588 Weathering Steel] 7000 PSI, 6 GPM, (48 kPa, 22.7lt/m), zero degree rotating tip, salt remover additive.
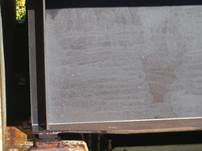
This Corten Steel beam end was high pressure water cleaned WITHOUT abrasion.
4. Hand Tool Cleaning (When pressure washing, or blasting are not allowed.)
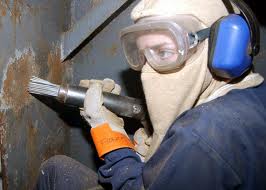
Needle guns and abrasive Strip disks 40 grit have proven effective at removing corrosion hot spots and under cutting paint as the applicator prepares for Spot Painting using HRCSA. [Always solvent wipe the steel substrate with compatible thinner before applying HRCSA chemistry.]
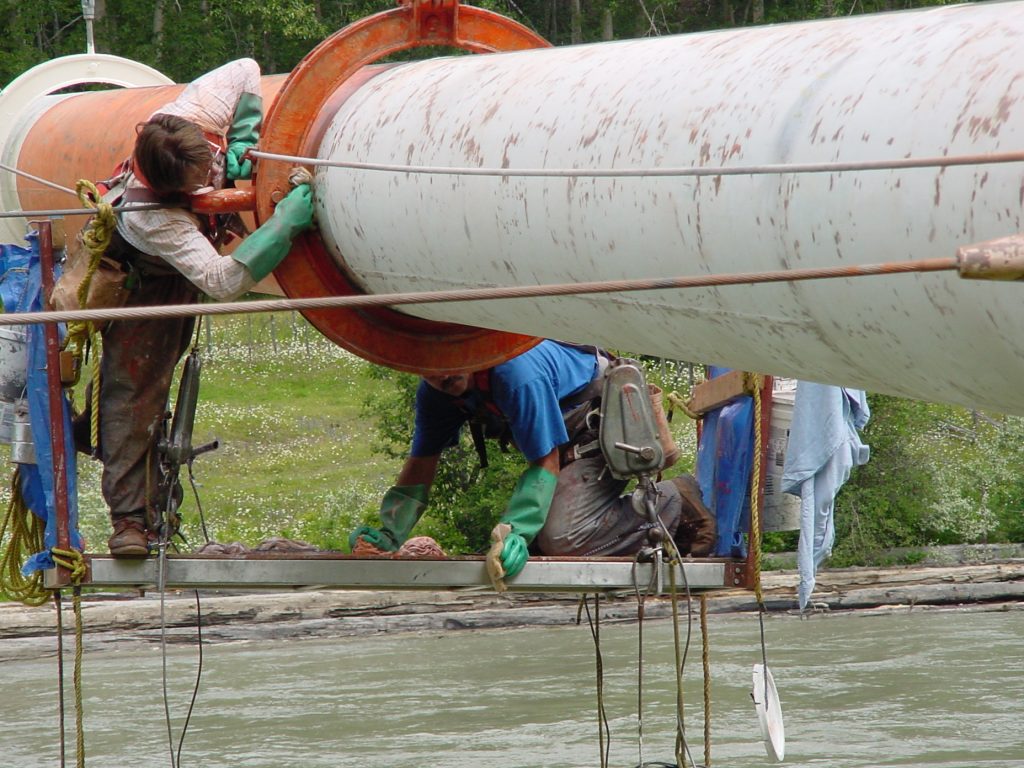
A quick sanding is usually all that’s needed to remove corrosion hotspots from flat surfaces. Bolts and rivets, may require some additional wire brushing. Once cleaned, simply solvent wipe the surface areas with a TRT01 solvent soaked rag to remove loose matter and reactivate the existing paint for better adhesion.
HRCSA Coating Application
HRCSA is a SINGLE COAT, single component, 2 step application coating. Click on the following link for details on the application of this high performance corrosion mitigation coating system: