What is ASTM D 5894 and what where the comparative results when HRCSA Primer/Topcoat was tested against the more commonly prescribed zinc, epoxy, etc. coating systems?
Revert to: 3 types of coatings for this answer.
What is the difference between OUTCOME BASED SOLUTIONS and PRESCRIBED SPECIFICATIONS?
Engineers are growing tired of specifying “Best Effort” in their field applications when what they would instead to find long term solutions for their steel corrosion problems.
When an engineer’s primary intention is to stop corrosion hotspots in ALL areas – including those where access is limited – areas like steel to steel interfaces (crevice corrosion), steel to concrete interfaces, bearing plates, pin connectors, more and more are realizing that their Prescribed Specifications are not able to achieve these objectives on all steel corrosion refurbishment projects..
In these days of limited budgets, more and more governments have begun reverting to OUTCOME BASED specifications which ultimately outsources the responsibility of providing field proven, long-term solutions to 3rd party consulting firms and contractors who through their own market research and experience have found chemically active corrosion control solutions that have been proven reliable enough for them to sign on to 5 year corrosion control warranties that include ALL types of corrosion hotspot zones – including crevice corrosion, pack rust and other “impossible” areas where rust tends to normally bleed from.
HRCSA is one such solution offering with over 30 years experience at chemically stopping crevice corrosion, pack-rust, corrosion-frozen bearing problems, wire rope problems all the while reducing the overall cost of deployment.
Can all crevice corrosion / pack-rust cells be chemically stopped?”
- Black oxides inside crevice-corroded and pack-rusted joints and connections has been chemically neutralized in the field has remained stable for 25+ years. This long-term performance is conditional on a proper salt-mitigation flush followed by the corrosion cell being blown dry with high pressure (clean, dry) air before treatment with The TR2200HS HRCSA Penetrant/Sealer.
Note: Tightly adhered affixed black oxides on flat surfaces need to be mechanically removed before coating otherwise the HRCSA Primer/Topcoat will cause the surface black oxides to dis-bond and fall off. - For corrosion at concrete/steel interfaces, wide plate bearings, leaking Q-decks, please contact your HRCSA representative for detailed directions on best practices.
Why won’t traditional coating or caulking work to stop active crevice corrosion /pack rust cells over the long-term?
Caulking does not work.
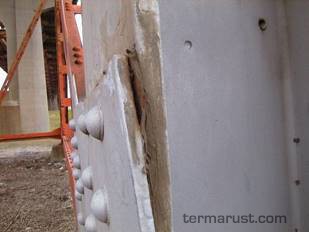
HRCSA meld coat after 17 years.
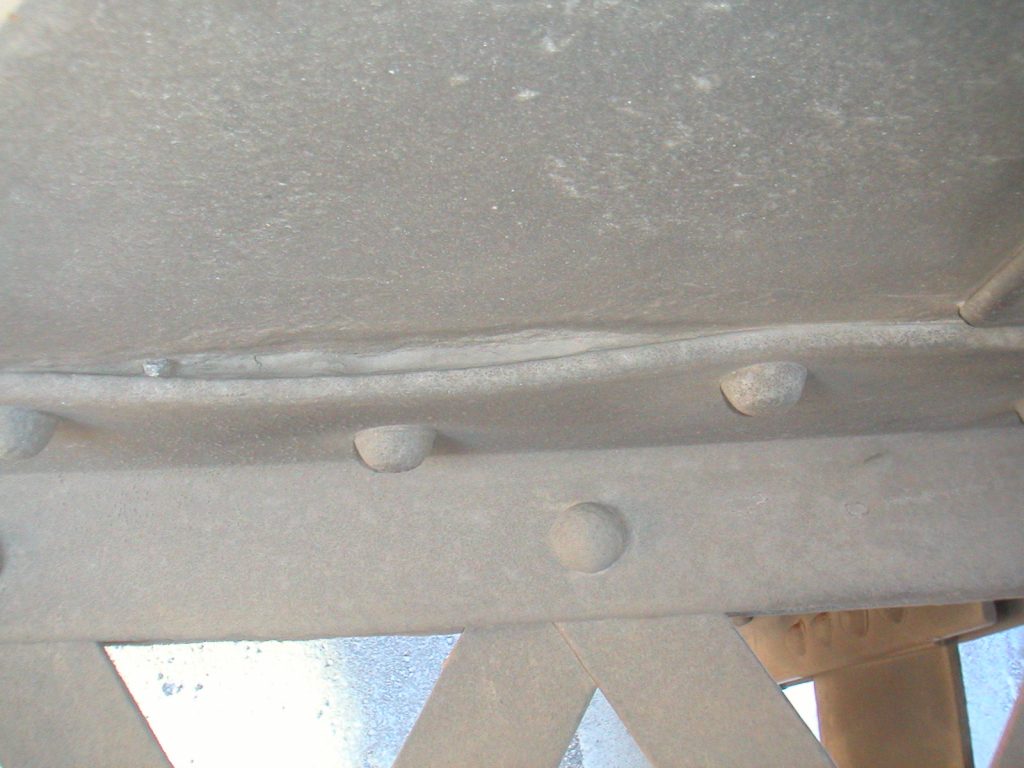
Masking (covering up with Coating or Caulking) an active crevice corrosion and pack rust cell does not stop the corrosion hotspot. This because the existing reacting hydrolyzed salts in the crevice form an acid (electrolyte) feeding the corrosion reaction which is dissolving the steel inside the crevice and converting it to black oxide. The trapped salts in the covered crevice actively draw moisture through the coating (all coatings have a moisture vapor transmission rates) to the residual salts inside the connection. To stop it, this chemical reaction must be neutralized else the corrosion reaction will continue and actually be accelerated. “Accelerated” means that, the oxygen-deprived crevice corrosion cells become even more acidic and damaging to the steel.
What is the difference between a 5-year Termarust corrosion warranty as compared to the more traditional industry paint warranties?
When applied to specification, the Termarust HRCSA corrosion mitigation warranty guarantees that the Coating’s HRCSA chemistries will stop ALL structural critical corrosion on steel structures including crevice corroded and pack rusted joints and connection (rust bleeding) with no exclusions.
“How much more effective is 7,000 PSI (48.3 Mpa) 6 GPM (22.7 liters) per minute hot water when compared to 5,000 psi (34.5 Mpa) 5 GPM (18.9 liter) cold water?
7,000 psi (48.3 Mpa) / 6gpm (22.7 liters) per minute hot water with a zero degree rotating tip enables the end-user to notably increase productivity (+30%) and reduce collectable wastewater they otherwise would have to treat by as much as 80% through evaporation, vapor removal and proper ventilation. . These higher pressures produce the most effective crevice, pack-rust, and pit corrosion flushing. They also increase production rate by speeding up the removal of suspect coating, High Pressure Water cleaned surfaces dry faster allowing less delays and quicker coating times.
How effective is 7,000 PSI (48.3 Mpa) 6GPM (22.7 liter per minute) hot water for high-pressure water cleaning A588 Weathering Steel?
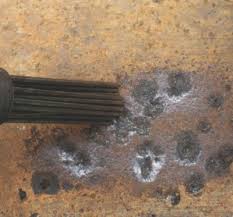
Weathering steel produces a thick protective corrosion patina layer which was intended to act as a protective barrier for the steel. When salt water comes in contact with this protective patina it converts the iron oxide to iron chloride which is soluble in water. Washing away the patina opens the door to renewed corrosion resulting in accelerated section loss and serious pit-rusting. Because pit rusting requires a very thorough flushing to ensure complete removal of bonded salts, it is recommended to first remove this salt contaminated corrosion buildup with needle-guns and/or introducing crushed glass media injection into the pressure water.
Was Termarust designed as a maintenance coating system or a Recoat system?
- When applied directly to clean or light to medium flash rusted steel Termarust’s HRCSA polar bonding adheres to steel substrates without the need for a surface profile – including steel that has 1/64th” of an inch or less surface black oxide. The only requirement is for the surface to have been salt mitigated as per the allowable limits in the specification.,
- Due to Termarust HRCSA’s Primer/Topcoat’s elastomeric nature it is rarely shop applied – due to risks of coating damage during on-site erection and transport. Termarust is an in-place maintenance coating for onsite rehabilitation projects on complex structures – especially those with crevice corrosion and pack-rust and/or for projects with tight budgets and/or narrow application windows.
- The wet abrasive blasting (crushed glass) method demonstrated on our website is field-proven and is being used to help expedite removal of thick, tightly adhered black oxide and to mitigate risks of recurrent corrosion reappearing where deep pit-rusting had taken place [Most corrosion coating failures occur in those areas where previous corrosion existed.] Some black oxide cells can be so thick that they can only be fractured using pneumatic-hammers or other mechanical means.
Can Termarust HRCSA Primer/ Topcoat be applied by brush?
The optimum way to apply Termarust HRCSA is by airless spray. If brush application is necessary, care must be taken to ensure that the proper wet film thickness is applied. Applying Termarust’s HRCSA (by brush) requires a laying up process (cross pattern brushing) to ensure film thickness consistency as opposed to brushing out processes which would be used in stripe coating. In addition, Termarust’s HRCSA primer-topcoat is thixotropic, application by brush may create brush marks in the applied coating. To minimize the brush marks apply using a cross brushing pattern to ensure full surface coverage and proper film thickness.
What steel substrates can HRCSA be applied to?
HRCSA (High Ratio Co-Polymerized Calcium Sulfonate) coatings, are designed and engineered especially for encapsulation (overcoat) of existing aged leaded paints, vinyl, aged coal tar epoxy, polyurethanes, epoxy mastics, organic or inorganic zinc, galvanizing, metallizing, acrylics, A588 steel, tightly adhered contaminant free rust, and Light to Medium flash rust or re-coating of new or prepared structural steel.
If applying Termarust HRCSA to offshore platforms where sea storms can arise quickly, how long must I protect the freshly coated surface to avoid water mist/spray damage?
As field conditions vary from site to site, one rule of thumb would be to protect the freshly coated surface until it is tack free. (the coating has been applied and rained on right after application with no longer term effect on performance). After the HRCSA surface is tack free (even if still elastic to touch). the risk of water damage to the coating is reduced dramatically.
This system is ideal for use over minimally prepared surfaces and is especially suited for coating of flexible structures [even wire rope – and bearings – and pin connectors]. Ideal for use with High-Pressure Water Cleaning. i.e.: 5000 -7000 PSI(34.5-48.3 Mpa) at 5-6 Gallons (18.9L to 22.7L) per minute preferably hot water – although some applications are best done by hand tool cleaning (wire rope as an example).
Why are (wet film-thickness) WFT measurements used instead of (dry-film-thickness) DFT measurements in all application videos?
For single component HRCSA Primer/Topcoat to thoroughly wet all micro voids in the steel profile (the most reliable chemical approach needed to prevent undercutting), the formulation’s slow curing, wet-on-wet properties also enables it to meld with HRCSA Penetrant/Sealer in the crevice corroded joints and connections to create a positive chemically active seal which cures through oxidation, UV exposure, and heat. [A single wet-on-wet application that involves a 1 coat, 2 step process that saves time.] This slow cure approach allows inspectors up to a 2-hour window to inspect WFT and request additional coating in areas which might have been missed or were too thinly coated.
How does one manage HRCSA Penetrant/ Caulk /Stripe / Overcoat applications with “single-coat” 3 or 4 step HRCSA wet-on-wet coating system?
1) Achieve the specified surface preparation requirements.
2) Apply TR2200HS HRCSA Penetrant/Sealer liberally under pressure into all crevice corroded and pack rusted joints and connections, including around bolts, nuts, and rivets wherever gaps have been created by crevice corrosion. Avoid application on surfaces other than in and around crevice corroded joints and connections. Excess Penetrant should be brushed out for a smooth, final finish.
3) Apply a TR2100 HRCSA “caulk-coat” / “heavy-stripe-coat” wet-on-wet directly into those HRCSA Penetrant/Sealer treated joints, connections, and gaps around bolts, nuts and rivets (maximum 30 to 36 mils (750 to 900 μm) WFT).
4) Continue to apply the TR2100 HRCSA Primer/Topcoat to Spot prime bare contaminate free or flash rusted steel [minimum of 5 mils (125 um) DFT (7-9 mils 175 to 225 μm) wet)] over bare steel and tightly adhered contaminant free rust and stripe coat sharp edges and corners.
5) Continue to build the thickness (TR2100 HRCSA Primer/Topcoat) with a ‘finish’ coat of TR2100 HRCSA Primer/Topcoat to an additional film build of 7-9 mils (175 to 225 um) wet over freshly coated surfaces and overcoat existing tightly adhered paint (where applicable).
What type of spray equipment do you recommend painters use?
- Airless spray pump. Best is 30:1-45:1 ratio pressure. [10:1 and 80:1 also seen in field use.] Airless spray tip: 17-23 (No smaller than 15mm).
- Conventional spray with a pressure pot use a DV -MCB gun or equivalent with a “D” fluid nozzle and a 64 air cap.
- NOTE: BRUSH, ROLLER AND PAINT MITT APPLICATION CAN BE USED AS WELL AS OTHER ACCEPTABLE SPRAY AND APPLICATION EQUIPMENT DESIGNED FOR LIQUID COATINGS.. CONTACT YOUR REPRESENTATIVE FOR RECOMMENDATIONS.
- When applying HRCSA to cold or high condensation situations (cold natural gas valve in a high humidity environment), reach out to your local representative for application methods.
Is saponification a concern with HRCSA?
NO. The HRCSA system is formulated in such a way as to not present any issues with the small percentage of alkyd co-polymer coming into contact with zinc substrates. The HRCSA Primer/Topcoat has been used to coat zinc substrates of all kinds for over 26 years without a single corrosion or coating performance warranty claim.
Are all calcium sulfonate formulations created equal?
Buyer Beware!! HRCSA High Ratio Co-Polymerized Calcium Sulfonate Primer/Topcoat and TR2200HS HRCSA Penetrant/Sealer rust mitigation system has a 30-year field proven history and is a pigmented type of co-polymerize reacted synthetic resin with a unique patented crystalline modification that cures by air oxidation.
HRCSA formulations provide better corrosion resistance, wetting properties, thixotropic (ability to resist runs or sags). Specifications should clearly define the percentage of active sulfonate and quality control procedures should be put in place to enforce the specification.
Unlike standard CSA coatings are Calcium Sulfonate Modified Alkyds – Similar to the silicone-modified alkyd wherein a small percentage of calcium sulfonate is introduced to enhance the properties of the base alkyd resin. Typically a low-cost, low-quality calcium carbonate filler with only a small percentage of active sulfonate added into the mix.
Download: CSA ≠ HRCSA to understand how to protect your steel refurbishment investment by specifying field proven HRCSA and not CSA coatings.
HRCSA: the Difference between Tack Free and Full Cure
The HRCSA Technology is the personification of the” long-lasting coating performance Golden Rule”. “The slower it cures the longer it lasts.” After application the HRCSA remains flexible even thought it is tack free to touch.
The coating can be touched and is not “wet”, the coating is “elastomeric (Flexible)”. (if It was wet it would have washed off in a heavy rainstorm like hit a structure 5 ½ hours after application. The coating is homogeneous immediately after application because of its thixotropic nature (only moves under pressure) and tack-free between 8 and 48 hours of it’s application depending on temperature, UV exposure and humidity.
The HRCSA coating will remain flexible. NOTE: The HRCSA primer/topcoat moves with the structure (has a high elongation factor of up to 700%) and therefore does not “harden and cure” like a traditional catalyzed coatings. This elasticity makes HRCSA coatings highly resistant to impact damage like chipping, cracking and undercutting.
When does the HRCSA coating become “Tack Free”?
HRCSA cures through UV, heat and oxygen. In hot, dry, climates on a sunny day, HRCSA applied coatings can be tack-free within as little as 3 hours. In cases where there is no sun, little heat and humid conditions, you might need to wait 18 hours or more before it will be dry to the soft touch (becoming firm will take longer). However, being a one coat / 2 step system applied wet-on-wet does not prevent the contractor from finishing and moving on quickly if his coating applications are planned with the right exit strategy.
How does HRCSA Penetrant/Sealer differ from other Manufacturers Low Molecular Weight Penetrants.
HRSCA Penetrant/Sealer is RAQ is 0 m3/minute as the product is 100% solids 0 VOC and throughout HRCSA’s 30 year history, neither air quality nor the risk of an explosion has ever been an issue.
HRSCA Primer/Topcoat is approx. 250 -275 g/L VOC and the solvent is low odor mineral spirits which in this formulation are slow release. Under normal conditions on a bridge, the HRCSA Primer/ Topcoat cures by oxidation and with the solvent being an integral part of the matrix (not an add-in like a thinner) they do not release quickly. Under normal working conditions, the formulation’s curing method will not provide any chance of enough concentration build to pose an explosive hazard situation.
Is there risk of explosion during the application of HRCSA coatings / RAQ (Required Air Quality)?
Air quality calculation:
Type of Ventilation, m3 air input per minute = [P*RAQA / t] where
P = paint to be used on the bridge steel surfaces, liters
RAQA = RAQ, (m3/l) for the paint
t = (application + surface dry) time in minutes
Note: The need for ventilation is highest during the paint application process when solvents evaporate both from the paint spray and the wet paint surface. Ventilation fans need only run until the coating is touch dry. When the coating is Surface (touch) dry the solvent evaporation, rate is much lower, and the fan speed may also be reduced.
Example HRCSA Theoretical Calculation (if there was a risk):
A 650 m3 containment interior volume has a steel surface coated with one coat of a 63.5 % Volume Solids HRCSA coating, at 250 μm DFT.
Assume the contained bridge has a calculated surface area to be coated of 1260 m2.
Application speed is 3.5 liters per minute.
Theoretically how much fresh air must be blown into the bridge containment per minute to eliminate a theoretical explosion risk?
The steel temperature is 23°C.
Answer: 250 μm/0.63.5 * 1260 m2 = 312 litres of paint.
This requires 312*60 = 18720 m3 fresh air. (312) liters / 3.5 litres sprayed per minute = 89 minutes application time.
Time to Surface dry (as per technical data sheet) is 12 hours at 25°C.
The average ventilation rate for the most demanding period is therefore 18720 m3/ (89*60) min = 34 m3/minute
RAQ Theoretical if there was a HRCSA explosion hazard.